Deburring Machine!
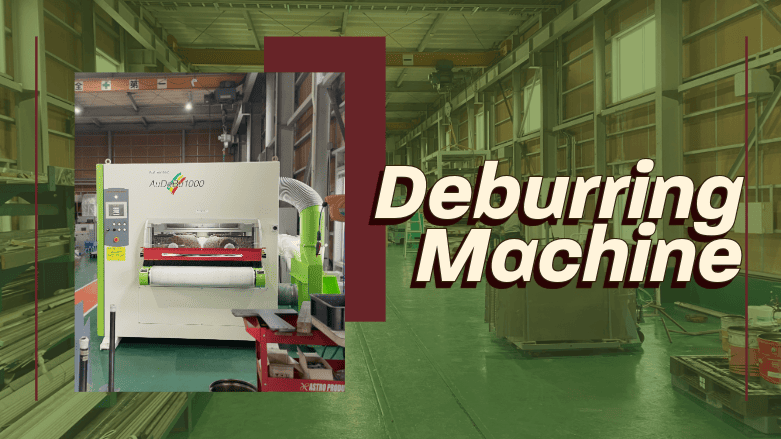
We have installed a deburring machine in our main factory!
Somewhat in a state of excitement, I would like to introduce you to our newly welcomed colleague.
What is Deburring?
Deburring is an essential process in sheet metal working. Why is deburring necessary in the first place?
There are two main reasons.
1. To prevent injury to users
When metal or resin is processed, burrs occur on the cut surface and other places. These are sharp edges where the base material is slightly raised or where minute metal fragments have adhered. These are surprisingly sharp and can cause injuries when touched with bare hands. Deburring is carried out to protect users from such injuries. This reason is of paramount importance.
2. To prevent interference with the manufacturing process and to ensure the quality of finished products
Burrs are inevitably created unintended parts and are of course not drafted on the design drawings. They may interfere the subsequent processes if left remained. Even if the product can be proceeded to a later process, it may not be assembled as intended or the size of the finished product may be slightly different, resulting in a significant drop in quality. This is another reason why the deburring process is essential.
Manual Deburring
Usually, burrs are removed using a sander. This process is simple but time-consuming and requires patience. Besides, I cannot say this in a loud voice but the finish depends on the skill and dexterity of the worker. Although it is not noticeable unless you put them side by side, if you are the type of person who is not bothered by detailed work, the result will be very beautiful, otherwise, ordinary.
The deburring machines was develped to automate this time-consuming and labour-intensive deburring process and ensure a uniform finish.
Deburring Machine
Model | AUTHENTEC AUDEBU 1000 AUTHENTEC Product Page |
---|---|
Max. Height of Workpiece | 20 mm |
Max. Width of Workpiece | 1000 mm |
No. of Brushes | 6 |
Rotation Speed of Brushes | 400 - 1200 rpm |
Circling Speed of Brushes | 5 - 16 rpm |
Belt Speed | 0.3 - 12 m/min |
Dust Suction Port | 250mm dia. |
Blower Discharge Port | 250mm dia. |
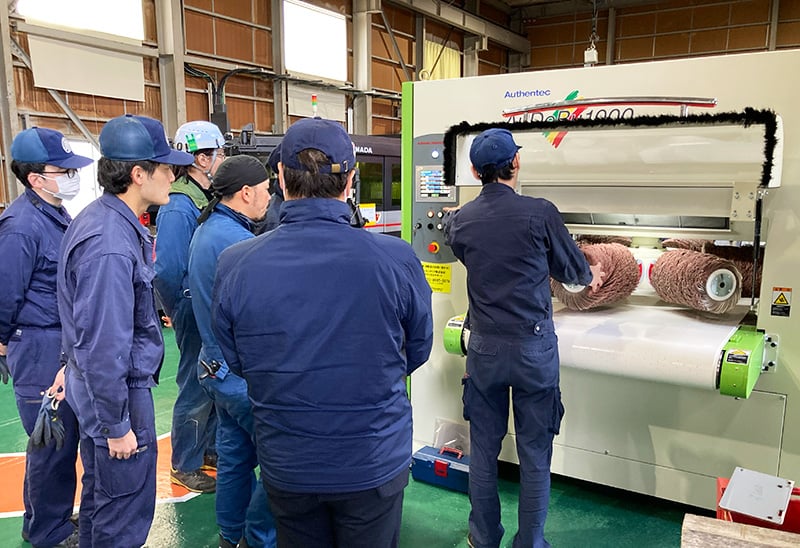
This deburring machine removes burrs by means of rotating brushes, and it can also perform round chamfering!
As the brushes lifting and lowering is mechanical, there is no risk of dust dispersal as with pneumatic systems, and brush replacement is a one-touch operation and requires no tools. Operator-friendly design, isn't it?
Let's compare the pictures of 'before' and 'after'.
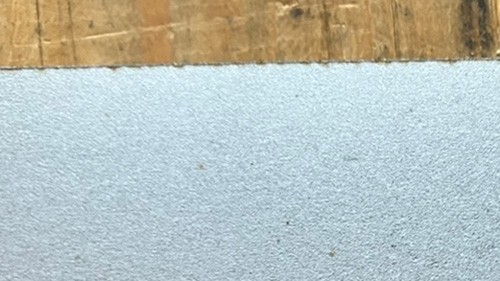
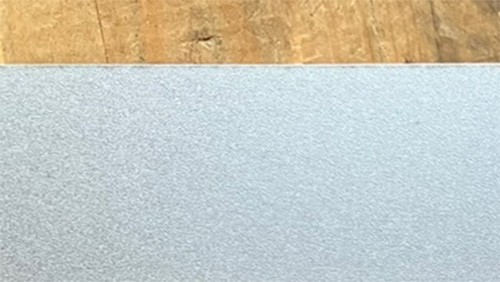
You can see not only burrs but heat tint have been removed completely. Beautiful, isn't it? No difference from handy work.
We hope this will hugely increase the efficiency in production processes.