Installation of Ultra High Dryness Unit 'KDS Separator + Electro-osmotic Dehydrator'
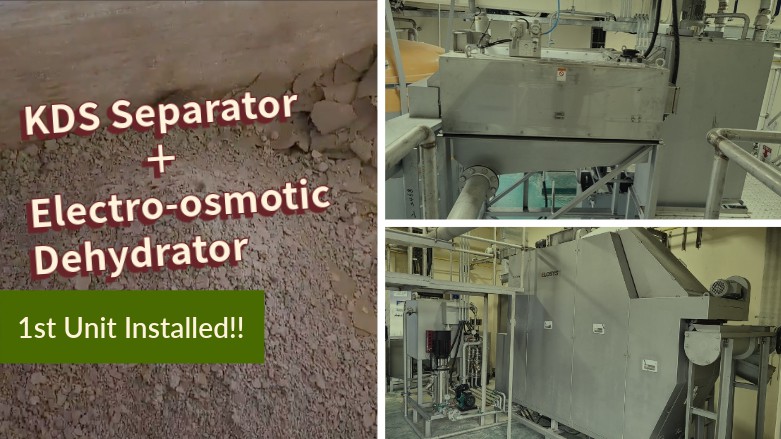
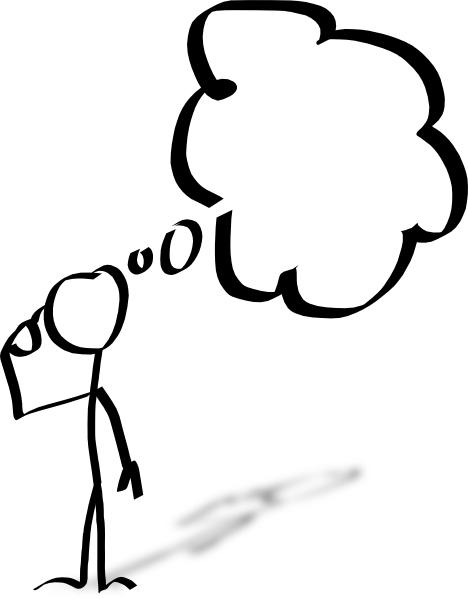
Designers of sludge dehydrator manufacturers, like us, are constantly thinking about
'How can we reduce the moisture content and get the cake drier!?'
while eating, in the bath, before going to bed and in their dreams...
(NOTE:Individuals differ, of course)
Volume reduction of sludge (to lower water content) is very important from the perspective of achieving carbon neutral in 2050 and reducing maintenance and management costs.
We, Kendensha, thought
'We'll halve the amount of dehydrated cake! That's the cake dryness of 40%! (60% moisture content)'
So, we have been exploring various options.
Amidst all this, like we have reported in our past post ("Reducing Sludge Cake by Half!", 6 Jan 2023), we have been developing a collaboration between our KDS Separator and electro-osmosis dehydrator for Japanese domestic market.
This time, we would like to report the first unit has been delivered not to Japan, but to neighbouring South Korea!
The site is a chemical plant and the target is their industrial wastewater.
The KDS Separator and electro-osmosis dehydrator were placed in the empty space of the existing filter press dehydrator, and the equipment was connected to each other by conveyors.
Hmmm, how three-dimensional!
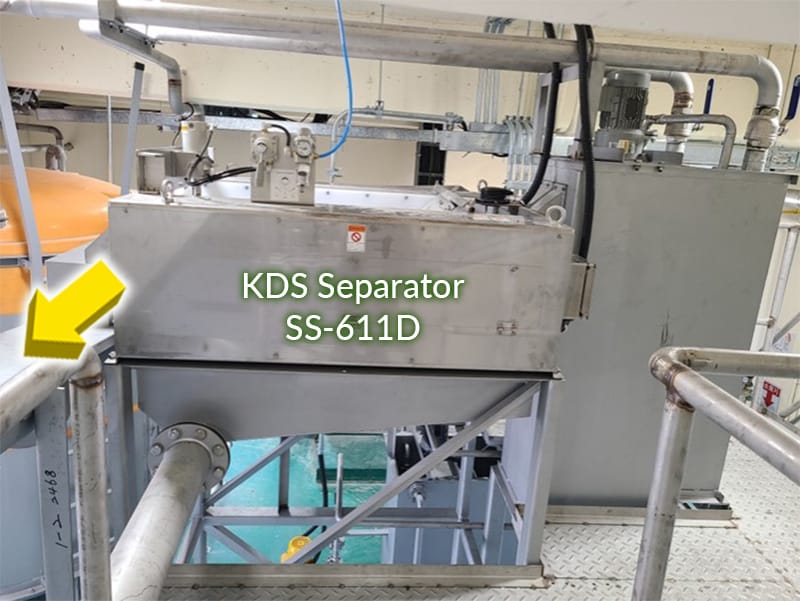
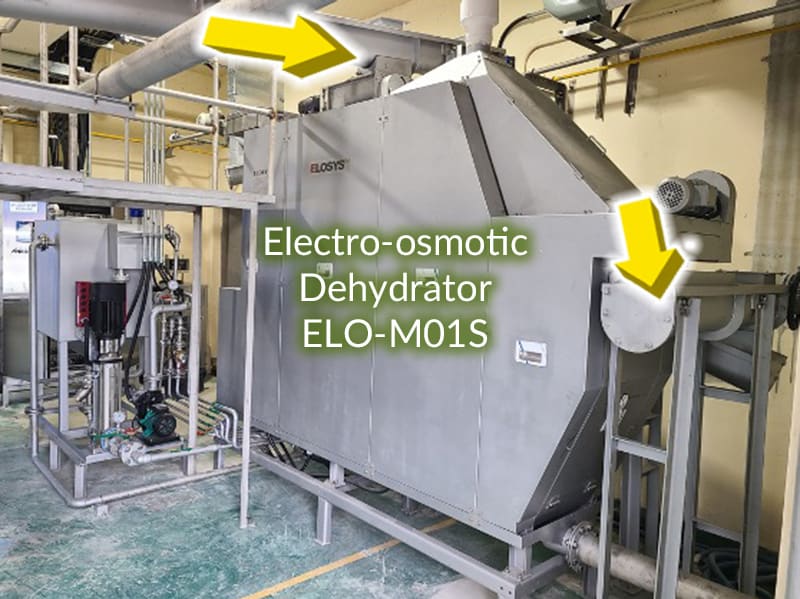
Now, let's look at the treatment situation
The sludge thickness was about 3% TS, the flow rate was about 1.3 m3/h and the throughput was 40kgDS/hr.
Sludge and polymer were fed into the flocculation tank and flocs are created by moderate agitation.
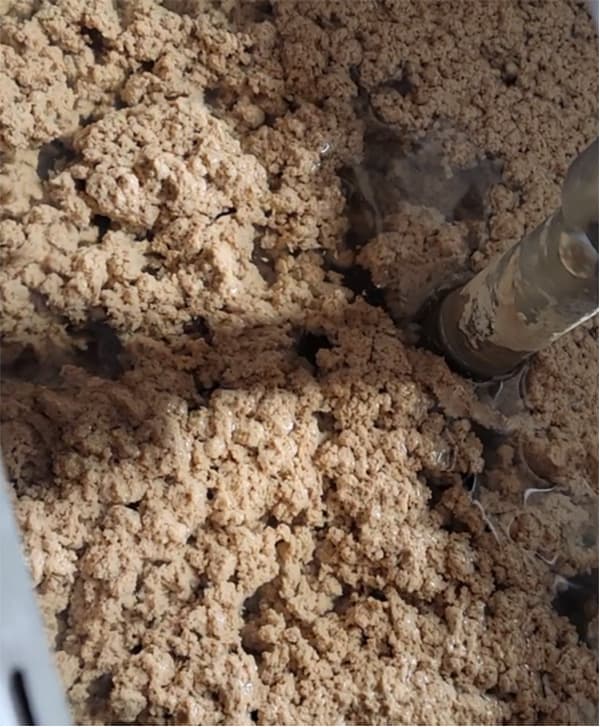
The flocculated sludge flowed naturally into the KDS Separator, where it was rolled by the oval-plates for thickening and conveying, and pressurised and primary dewatered by the pressure plates in the latter stage.
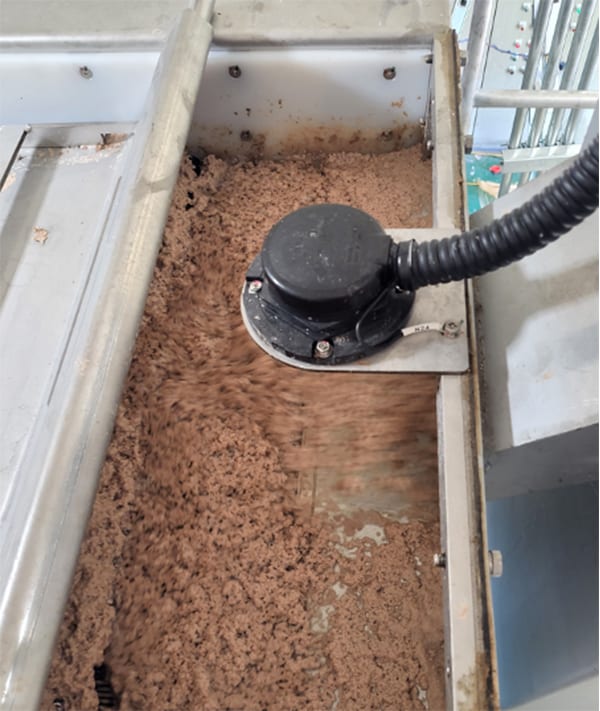
The KDS Separator (primary dewatering) dewatered very well, with a cake moisture content of about 71% (29% dryness) at the discharge.
The cake was then conveyed by a screw conveyor without shaft to the electro-osmosis dehydrator for secondary dewatering.
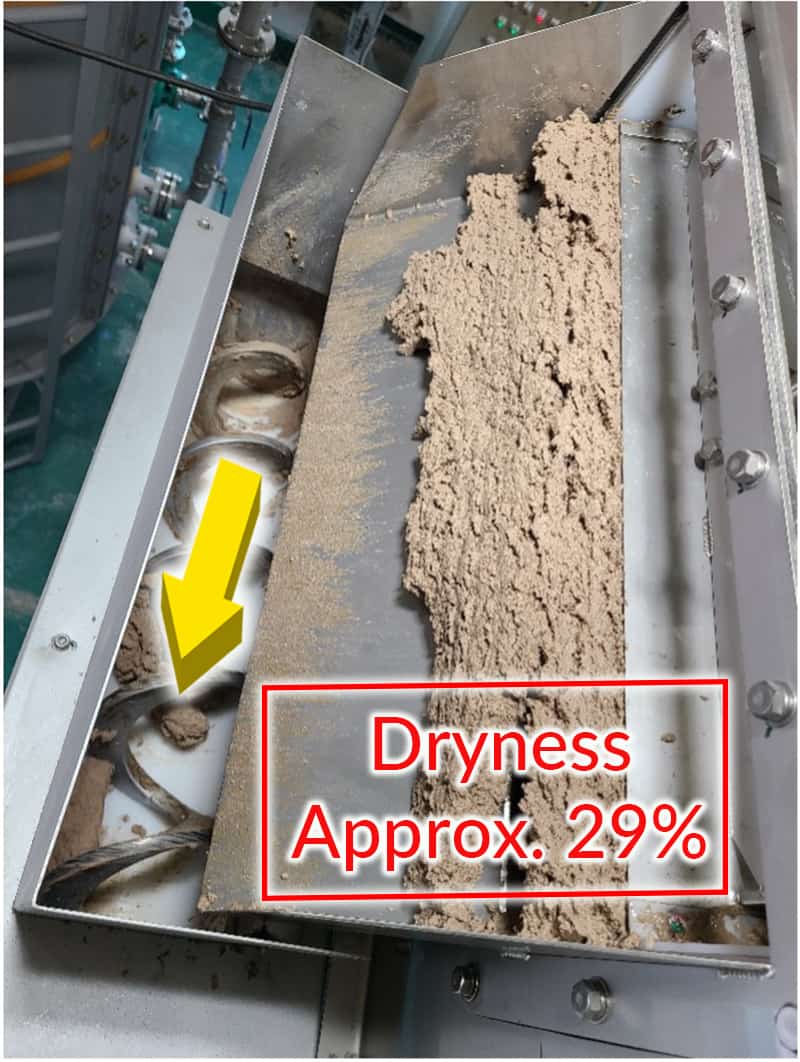
The discharge cake moisture content of the electro-osmosis dehydrator (secondary dewatering) was approximately 60% (40% dryness).
The cake was then conveyed to the existing yard by another screw conveyor without shaft.
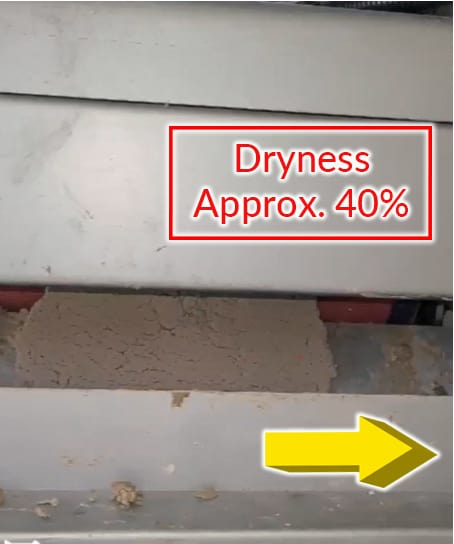
The image below is the dewatered cake in the storage yard.
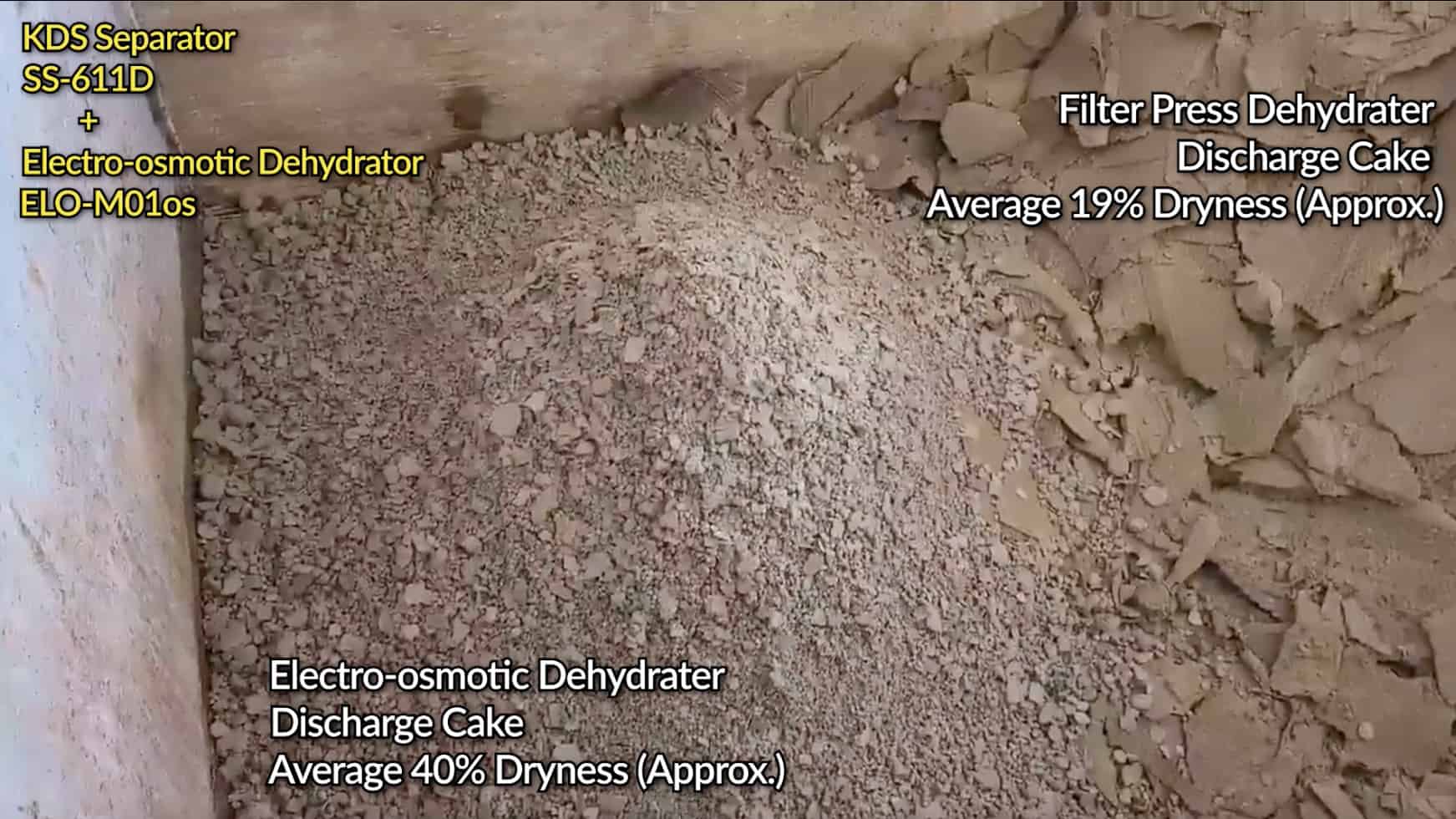
On the left is the cake after the KDS Separator + Electro-osmosis Dehydrator (moisture content approx. 60%, 40% dryness) and on the right is the cake from the existing filter press dehydrator. The cake dryness varies depending on the operating conditions and is approximately 15-25% (average approximately 20%). The cake from the electro-osmosis dehydrator is much drier, so it is crushed during transport and becomes smaller. Therefore, the bulk density is also larger and the volume of the loading bed of the haul-out vehicle is smaller.
To conclude, please play the video of the whole process!
Performance Summary
Existing System | |
---|---|
Throughput | 40kgDS/h (2m3/h x 2%TS) |
Cake Dryness (Water Content) |
34%±4 (66%±4%) |
Test Operation Result | |
---|---|
Throughput | 40kgDS/h (1.3m3/h x 3%TS) |
Cake Dryness (Water Content) |
higher than 40% (less than 60%) |