Processing Thick Plates
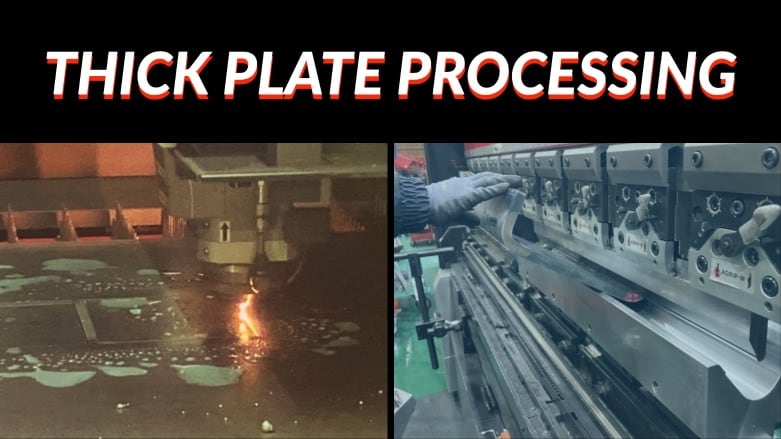
Last week, we added new settings to the fibre laser machine. (To be precise, this was done by the manufacturer of the machine, AMADA. Thanks for coming and doing it for us.)
This is because, for the development of new products, it has become necessary to process thicker steel materials, which we have not handled before. Generally, the thicker the plate, the more difficult the processing becomes.
In this post, we report on our first attempt at processing thick materials using the laser processing machine and the press brake. Metalworking jargon will appear here and there, but please look through until the end.
Laser Processing
We attempted oxygen cutting of three thicknesses of SS400 (a commonly used and relatively inexpensive general structural steel), 16 mm, 22 mm and 25 mm. Then, excessive combustion, which is one of the factors that deteriorate quality, occurred. This is a phenomenon in which iron in the base material reacts excessively with the assist gas (oxygen), causing the cutting groove to extend beyond the laser beam's irradiation area. This often occurs in thick material processing.
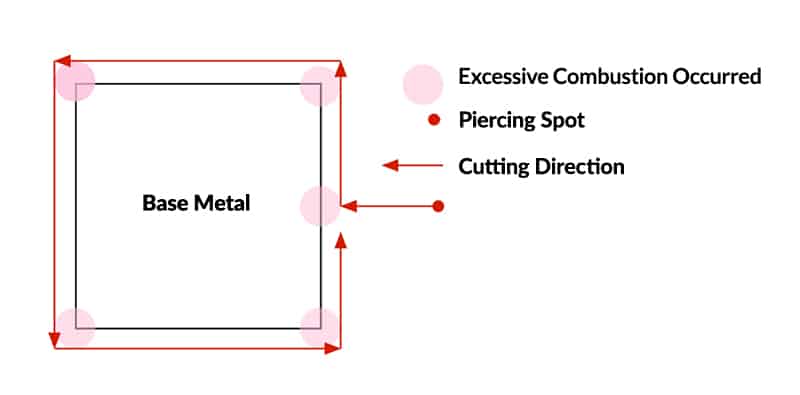
To prevent this, we took three measures.
- Cooling the base material with cooling water
Our fibre laser processing machine is equipped with a mechanism for discharging cooling water into base material. - Change of processing conditions
We reduced the temperature rise of the base material by intermittently processing the material with periods of non-processing (periods when there is no temperature rise due to the laser beam) during the laser cutting. However, as this method increases the time required for one process, it will be necessary to find the optimum solution by determining the balance between QCD (quality, cost, delivery/production speed) in the future. - Changes in processing procedures
We altered the piercing spot (where the hole is first drilled) and the cutting direction.
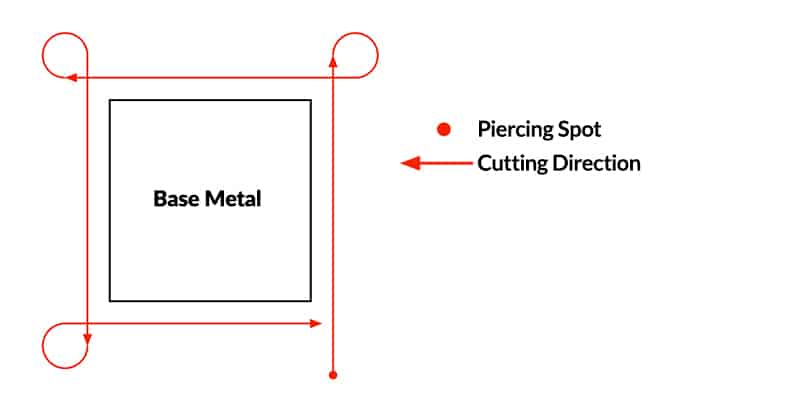
As a result, the excessive combustion was eliminated. Apart from excessive combustion, another problem that tends to occur in laser processing of thick materials is that the tapered shape of the cut surface becomes pronounced.
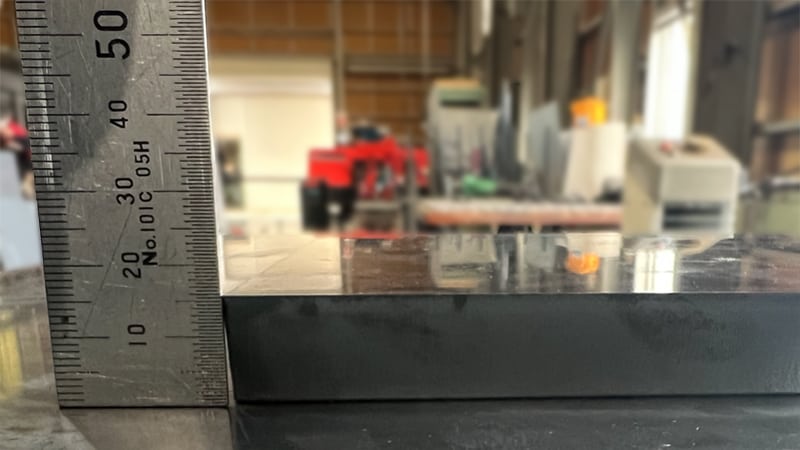
Although fibre laser cutting is characterised by a small taper effect, in this case it was angled at 1-1.5 degrees.
The designers need to take note of this.
The precise setting of conditions is a future challenge, but the result seemed to be less dross (ball-like molten metal that adheres to the back surface) and little droop on the cut surface.
Bending
Next, we used the press brake to carry out V-bending (bending by pressing into a V-shaped die) on the SS400, 16 mm thick plate, which had just been cut using the fibre laser machine. The 125 mm wide V-die cannot be set manually as it is quite heavy in total length. For this reason, it is divided into shorter sections and used side by side. However, one of these divided sections still weighs 41 kg.
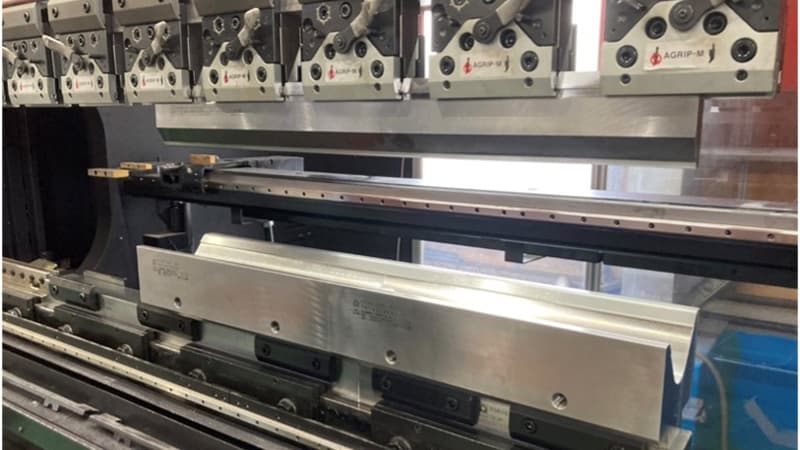
We applied a load of 1322 kN to a steel plate 270 mm wide, and measured the elongation value and spring back value (the elastic recovery of the base material to return to its original shape when the upper die is raised and the pressure is removed) generated during plastic deformation.
By correcting and setting conditions for these elongation values in the CAM, we will be able to formalise the tacit knowledge often associated with skilled engineering.
In addition, the bending of thick materials results in large 'bending humps' on the machined end faces. These bending humps can affect subsequent processes and are usually removed by sanding or other means. However, by calculating the amount of bending humps and cutting in to the material, for instance, a half round shape accordingly, the sanding process can be eliminated.
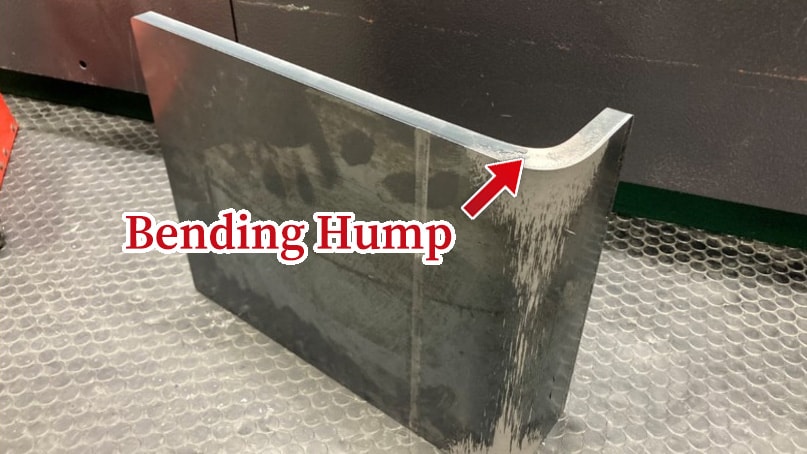
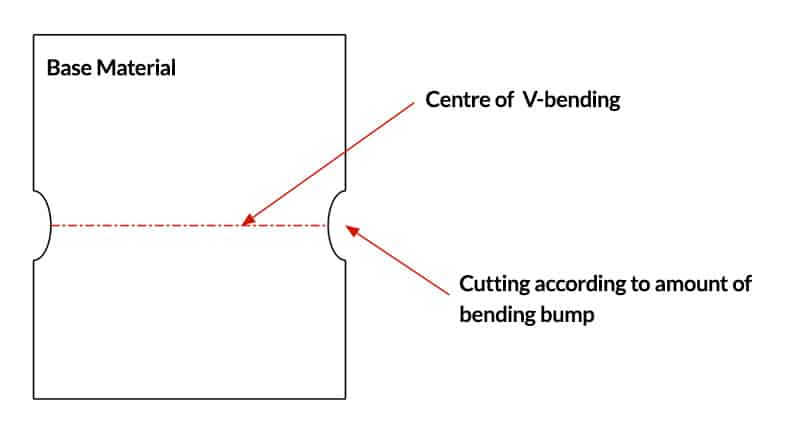
In order to ensure the perfection of new product, we hope to find the best processing method by trial and error.